Laser Alignment of a Reciprocating Ram Inside a Bore
Background
The customer is faced with an application for aligning a reciprocating ram that moves into a cylindrical bore for forming aluminum parts. There is a question if the motion of the ram is linear and thus parallel to the axis of the bore, and if the ram is showing signs of unwanted rotation during its stroke. These factors bear heavily on the wear and maintenance of the forming equipment.
Equipment
The customer selected the Microgage 2000 Machinery Alignment Kit because it is compact, easy to use, and can be set up with their application quickly — even in the field, if necessary.
Solution
The first task is to check the straightness of the ram’s travel to verify that the ram is not shifting in the vertical axis or the horizontal axis during its stroke. For this simple measurement, the Microgage Laser was attached to the ram directly. The Microgage receiver was moved down the exposed portion of the shaft to verify that the laser beam is parallel to the ram itself. The Receiver was then placed vertically on the Precision Tripod Mount and zeroed. The system was powered up and the ram moved through its full stroke of about 22 inches.
There was a slight change in the Microgage readings, indicating a minor vertical displacement during the ram’s motion, but the motion was considered acceptable. The ram was returned to its starting position, and the Microgage Receiver turned onto its side for the horizontal measurement. Again, the ram was moved through its motion and significant lateral shifts were detected. In examining the magnitude of these motions, the customer believed that the ram was turning during its stroke. A keyed mechanism was added to minimize the rotation, and the second pass indicated negligible shift in the horizontal axis.
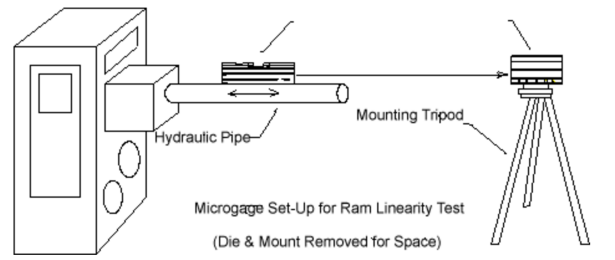